Order Sequencing solution for complex customer requirements
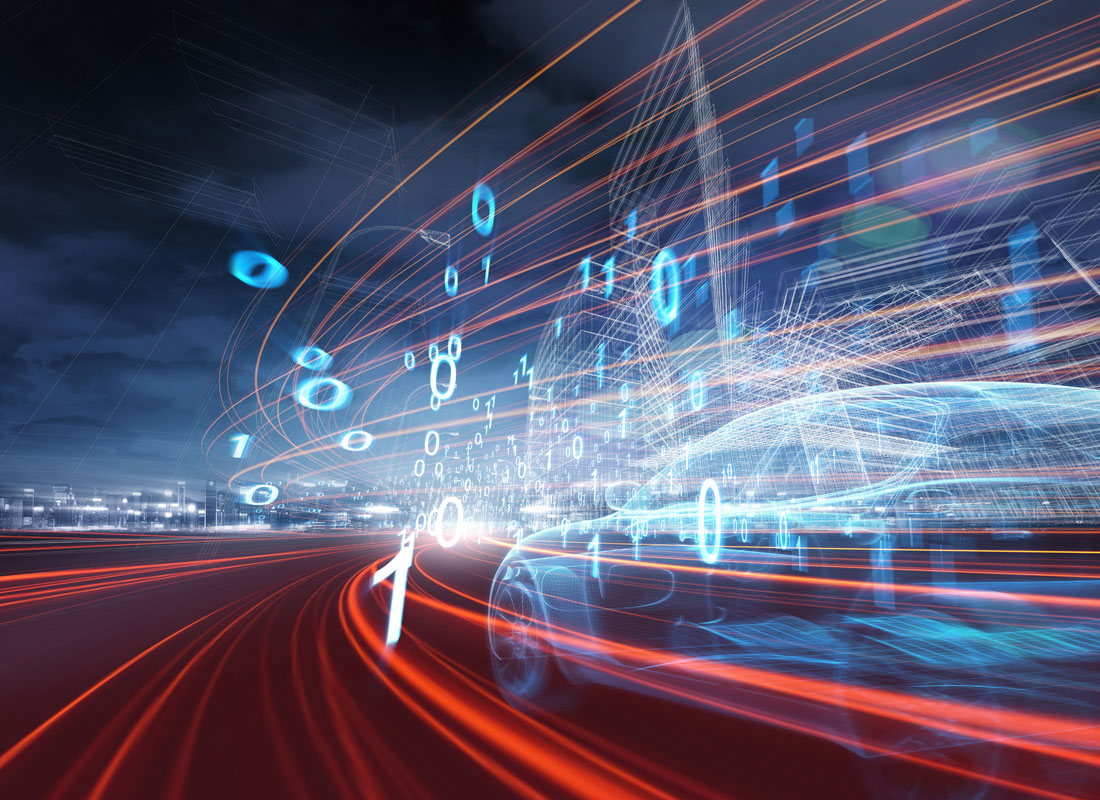
Status: Production lines are newly planned
A German sports car manufacturer is planning two production lines as well as four additional component production lines for engines and axles, each production line being subject to different requirements. In addition, a fifth component will be produced for vehicle interiors and seats. A suitable APS system is being sought to optimize lean management and effective production planning.
Challenge: Optimal control of external and order-related production
Both anonymous and order-related component production is to be implemented on the production lines. In planning, the order components should be optimally synchronized. In addition, it should be possible to control external requirements for the main sequences. This means that there are always special cases in planning, for example, when spare parts production with different production sequences is inserted. In addition, numerous variables must be taken into account when calculating dates: For example, the throughput times per combination of order and workstation are variable and are calculated differently at different stations.
Solution: Customized Order Sequencing concept
After a detailed analysis phase, in which all interrelationships, restrictions, and process sequences relating to the production lines were considered, the flexis experts developed a customized concept for a separate Order Sequencing solution for each production line. The Order Sequencing takes into account, among other things, the workload, target dates, and the necessary block and distance restrictions, as well as various equal distributions.
The complex deadline calculations are supported by a scheduling solution: This calculates and monitors the current factory status and the planned and unplanned orders. All these key figures are aggregated in reports and made available to the customer's downstream systems.
In addition, the software modules contain special monitoring tools for the evaluation of throughput times including a plan/actual comparison as well as corresponding control model evaluations; this supports the planner in the creation and maintenance of the complex control models by incorporating real order data.
Result: Stable production
All complex customer requirements are taken into account with the new Order Sequencing solution. Orders can now be conveniently and stably fed into the production line with an extremely customer-specific Order Sequencing and reference Order Sequencing solution. Despite complex scheduling rules, orders are optimally scheduled on the production lines without violating restrictions and rules.