Order Sequencing solution ensures compliance with all restrictions
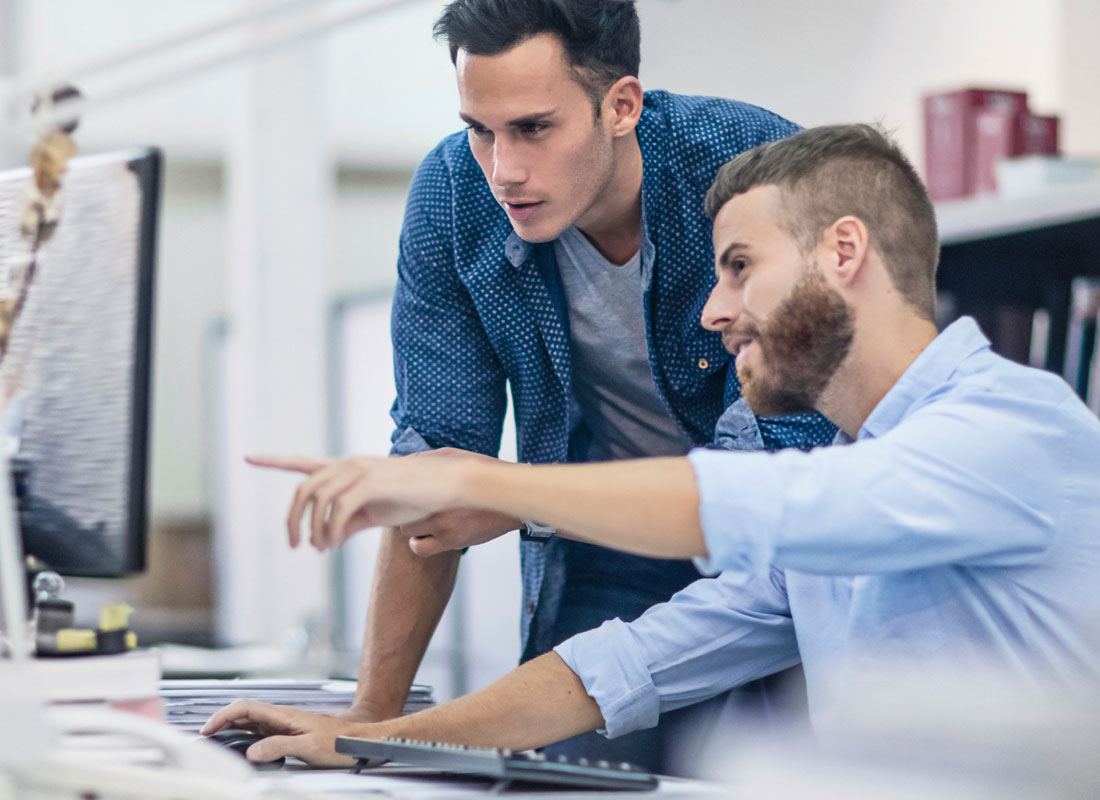
Status: Weekly Order Sequencing for multiple European plants
A supplier of forklift trucks, warehouse equipment, and automation technology creates weekly sequences for production orders with variant characteristics in several European plants. Lead times of four weeks are taken into account in the planning. Production planning managers want to implement an APS system that meets the requirements of lean management and "just in sequence" in every respect.
Challenge: Order scheduling in compliance with restrictions
The Order Sequencing of customer orders for production over a period of four weeks on up to 10 lines needs to be optimized, taking into account restrictions regarding capacities, deadlines, and workload. In this way,the sequence planning and thus production control need to be optimized. The solution is to connect to the existing SAP system. Goal: Continuous definition of the best possible order sequence, taking into consideration all assembly and procurement restrictions.
Solution: Perfect fit for the customer’s requirements
lexis’ team of experts developed a concept for an Order Sequencing solution with Springer evaluation and workload analysis tailored to the customer’s requirements. The sequences are visualized in shop floor management, e.g. band status and band overview. Employees can see the progress of the planning and the workload of the assembly line.
How does it all work? First, the routings or operation lists are read in for each production order. Then, the routing lists all operations that are carried out to manufacture a product. For each operation, the system displays which production order is planned at which work center and which standard values were used to determine the dates or the workload.
Result: More flexibility and tangible savings
With the flexis Order Sequencing solution, order sequences can now be optimized while adhering to all restrictions. This results in a number of benefits for the customer:
- Visualization of the planned sequence on the shop floor
- Choice of line and planning horizon
- Graphical display of the plan sequence and various reports in the browser
- Comment function
- Band/segment managers can obtain information about upcoming sequences and effects at an early stage
- Use of a uniform solution in six different plants with up to ten tapes each, resulting in a high degree of scalability
flexis’ solution makes the complexity of the processes manageable in a standardized way. The customer can now reliably meet targets. The employees in the planning area benefit from interactive customization options via drag & drop and are therefore extremely flexible. In this case, rapid concept testing contributed to the smooth implementation. In the meantime, the actual value-added chain can be traced via the standardization of the work processes - making tangible savings visible and obvious.