APS - Order Slotting & Scheduling
flexis Order Slotting & Scheduling helps to have an earlier available visibility, one of the key things manufacturers these days need for setting up optimized smart factories. flexis Order Slotting & Scheduling helps companies to get ready for industry 4.0: In a smart manufacturing process, the software system needs to mediate real-time data between sales and production, levelling and smoothing all production orders with a medium-term planning background. This is what flexis can provide by digitizing all data of manufacturing, making the availability of resources transparent. Transport planning is coordinated according to material requirements and transport slots within international supply chains. This enables real-time traceability of daily planning.
Outcome
Efficient and reliable production means that savings can be realized quickly. The multiple-point solution generates continuous improvements on in the efficiency of production processes.
Benefit
APS system with multiple point solutions can be used for various plants or production areas for midterm and short-term planning and even granular short-term planning. Real-time visibility by rescheduling and resequencing.
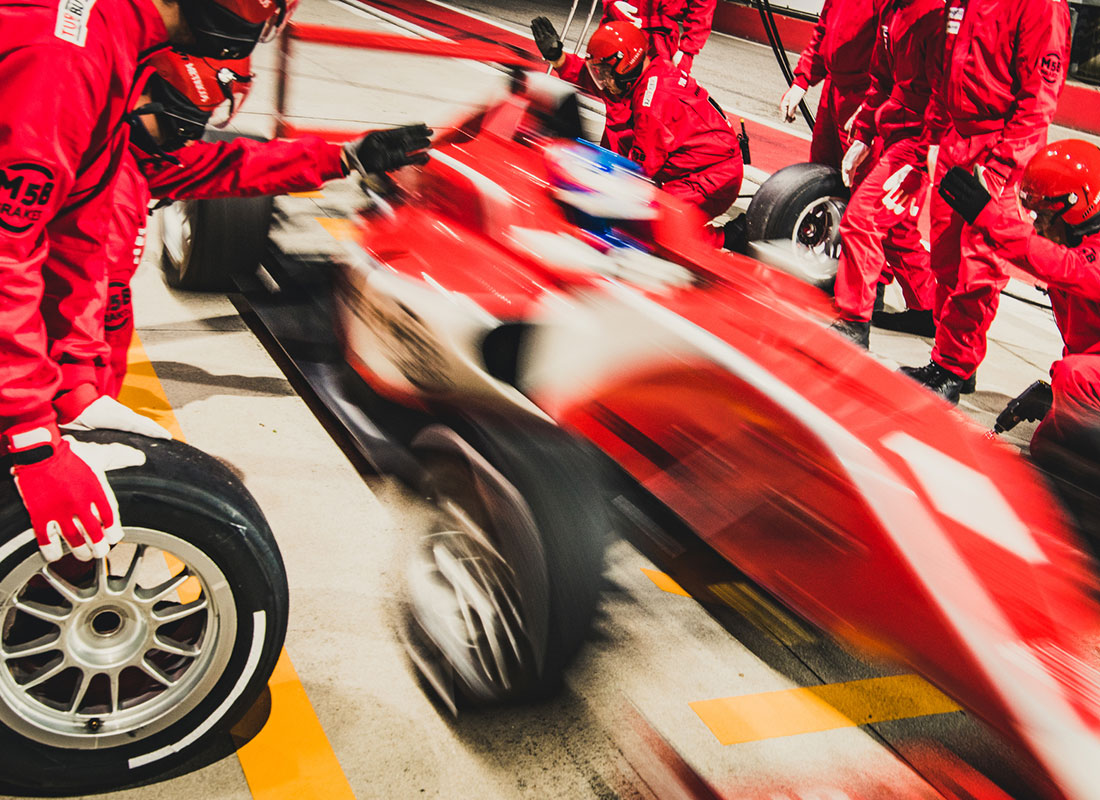
Detailed Description
flexis Order Slotting & Scheduling provides automated information about workflow in the order center, the sales view, and the production view. The production planner can see the current medium-term planning horizon in the order center. The software shows new orders and changes, while possible scheduling dates are displayed. The agent can trigger optimization order planning as required (e.g., in the case of sudden special orders). The sales view shows job sites for certain order configurations and prioritizes the orders (e.g., according to desired delivery dates). The production program preview visualizes assembly capacities and ensures reliable and balanced resource planning.
Typical challenges such as
- excessive warehouse capital costs
- slow reaction times to changes
- lack of transparency, e.g., about supply or resource bottlenecks
These challenges can be significantly improved by the flexis APS solution. Alarm functions in shop floor management ensure early detection of disruptions. This provides a solid basis for rescheduling decisions. The APS system generates a proposal for the largely equal distribution of orders, with the option of manual rescheduling via a drag & drop function.
Added Value
- Scalable, fast ROI due to easy implementation
- Integrated analytics supports rapid decision making
- Continuous improvement of processes
- Sustainable, reliable statements to the customer, increased in on-time delivery
- Full supply chain optimization allows reduction of current stock and finished goods inventory
- Increase in productivity through the equal distribution of work content
- Reduction of personnel costs
- Reduction of the necessary flexibility on the procurement side
- Cloud native SaaS Solution
- The order slotting solution provides even more benefits when extended with a JobShop Scheduling Solution or a Sequencing solution
flexis solution overview
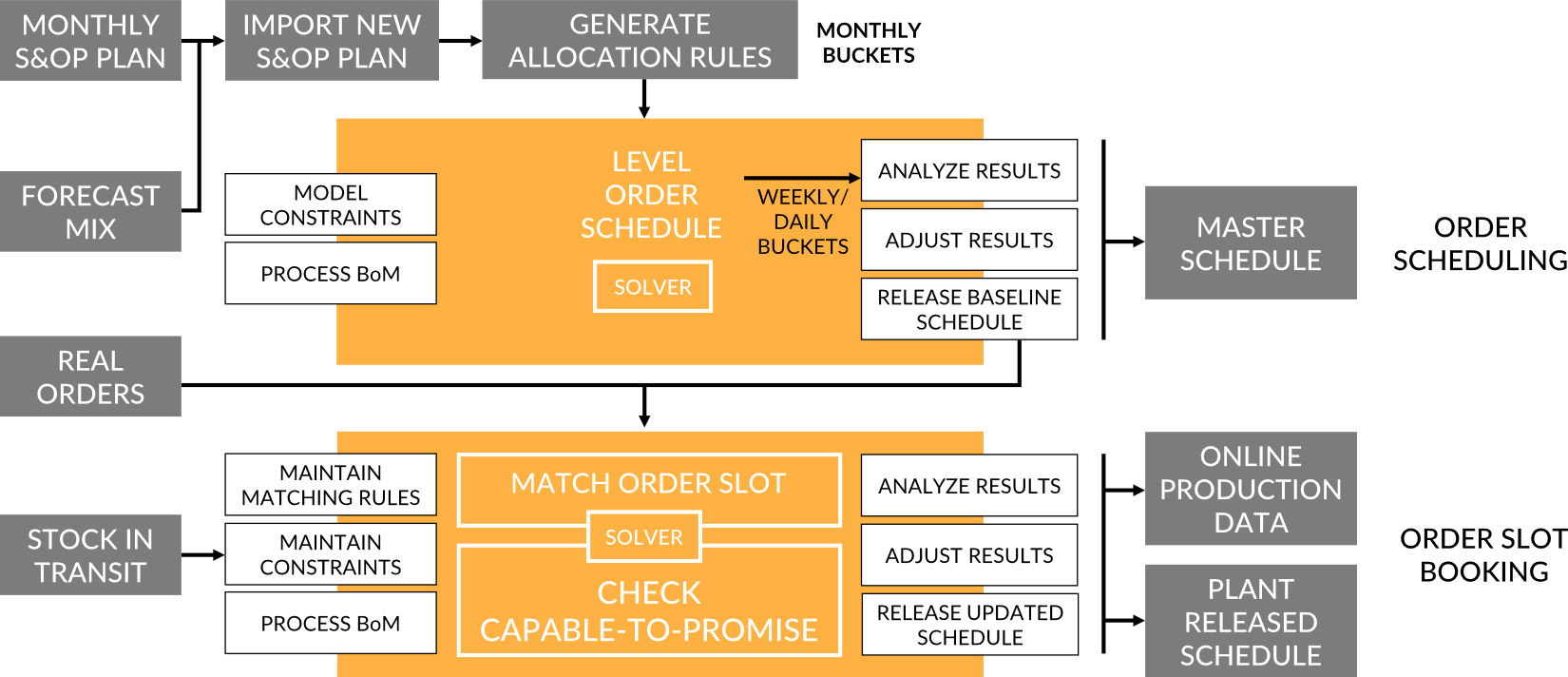