Triple Efficiency Increase through Multi-Modal Logistics Planning
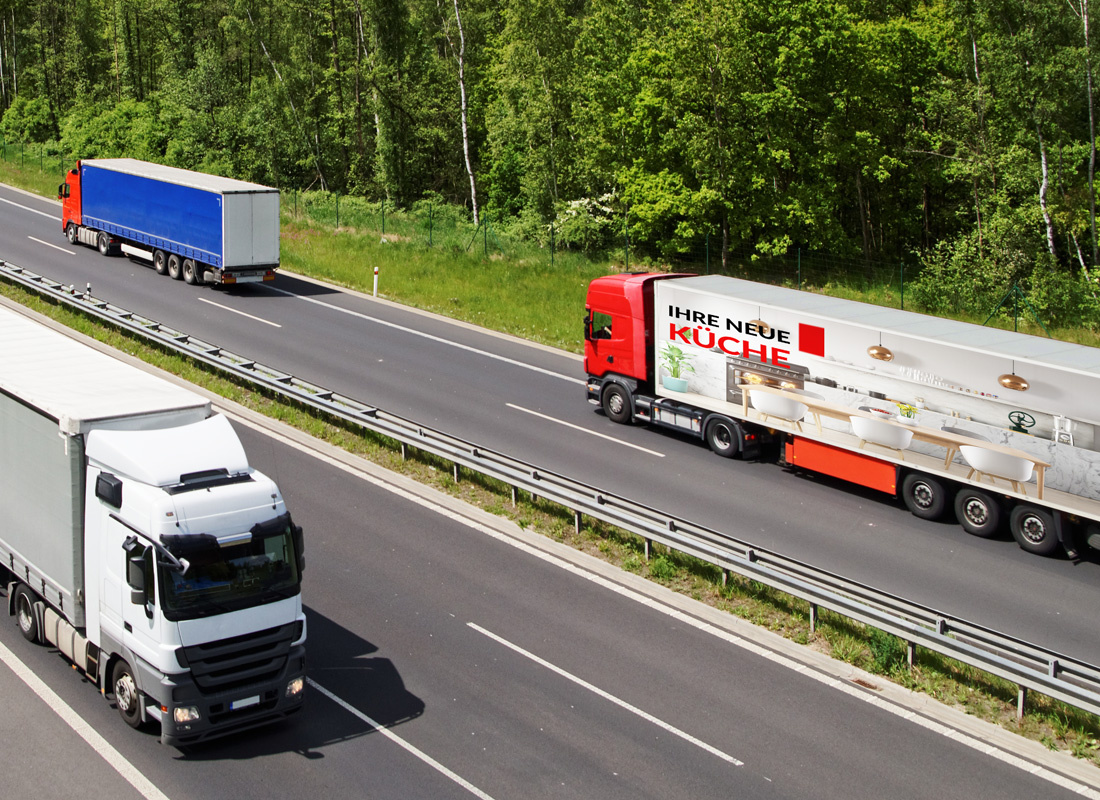
Savings in CO2 emissions, costs, and personnel
Kitchen manufacturer with state-of-the-art production standards and a demand for design, function, quality, and perfection. Sustainability, value orientation, and employee motivation are firm pillars of the company's philosophy.
Status
The German kitchen manufacturer delivers high-quality kitchens throughout Europe with a fleet of approximately 120 trucks. In the past, orders were loaded onto trucks and distributed to the regions via various tours. The empty vehicles then returned to the factory. The manufacturer delivers its orders exclusively via its own fleet of vehicles. This has the advantage of the factory-associated drivers being in direct contact with the customer. As a supplier of an exclusive kitchen brand, branding of the company-owned trucks is part of the corporate strategy. This strengthens trust and leads to a better delivery service. Transport planning is always done in consultation with production and on a weekly basis.
Challenges
-
Manufacturers of sensitive and valuable goods are usually reluctant to work with 3PL partners for the reasons mentioned above. In the application described, the manufacturer produces and delivers the kitchens in a fully assembled state, which requires increased caution during transport. This makes it all the more important to work with reliable and trained truck drivers who handle the delivered products with appropriate care and are attentive during transport.
-
Due to the shortage of drivers in Europe, the company needs to make improvements in transport management
-
The company's management is placing increasing emphasis on sustainability for a variety of reasons. Therefore, the company not only controls the cost efficiency of truck tours but also the total CO2 emissions and corresponding possibilities for reduction. Legal regulations with impending penalties but also customers who value CO2 reduction measures are pushing for action.

Solution
Use intermodal transport to improve costs, CO2 emissions, and transport efficiency. Why do 15 to 20 trucks have to go to Italy every week?
Are five vehicles traveling to Italy with loaded trailers sufficient if another ten loaded trailers were transported to Italy by train (or rail freight?)?
Thus, the five trucks in the country can take over distribution in this delivery region. However, this only works if the routes and tours for the orders were optimally planned in a time span from Monday to Friday. Based on the orders to be delivered, the flexis solution calculates how many trucks need to be dispatched to the region, considering all restrictions that the company specifies (truck size, loading times, delivery points, vehicle availability, etc.).
For the 15 trucks, the flexis algorithm suggests the best routes and tour structure in the delivery region. After optimization, the flexis software shows which tour ideally takes over the direct transport from Germany to Italy to swap the empty trailer with a full one after the first stop at the train station, and to deliver the next tour. The system optimizes the complete weekly planning, for example when to exchange the trailers or which tours are necessary to finally, after one week, drive back to the plant in Germany with an empty trailer.
What tasks does the software system perform?
-
Takeover of all shipments from the ERP via interface
-
Calculation of the optimal number of tours
-
Ideal tour design and determination of assets quantity
-
Definition of the best combination of different tours, matching the travel times and time windows
-
Consideration of train schedules with departure and arrival times.
-
Planning of shuttles to the trains - transport of full trailers from the plant to the station
-
Routing via predefined waypoints (e.g., regarding customs clearance by customs agents at certain border crossings)
-
Show all planning with one optimization software run
-
Possibility of manual rescheduling
-
Manual planning and support functions, for example: Calendar functions with closed days, holidays, etc., Visualization of production utilization on different production lines.
Result
Fully automated intermodal decision making and combination planning with maximum cost efficiency and planning reliability for deliveries. This agile project is executed in a timeframe of 9 months and includes the organization's data integration and business process customization.
Triple Efficiency Increase through Multi-Modal Logistics Planning